由于丰田的成功,自上个世纪末,有越来越的企业学习丰田生产模式,导入精益制造(原来叫精益生产,后来扩大范围到整个制造周期)。但是真正成功的,并给业务带来实质性提升的企业没有多少。 而更多的公司,工厂或者是搞了一段时间的运动,然后将精益丢弃一边,或者是只保留了精益的形式,固定的表单,报告,反而变成了对运营的负担。通过观察反思这些不成功实施卓越运营的工厂和企业,大概可以发现以下的问题:
企业负责人过度相信流程,系统以及模式的作用,而忽略了人这个至关重要的因素。 经常被大家忽略的一个现实是,在丰田生产模式中,员工的忠诚度和贡献度从来不是一个问题。在日本本土文化中,往往推崇的是“终生职业”。而众多的欧美企业和国内在学习丰田生产模式时,没有意识到文化差异以及员工参与度的差异,没有更好的发挥员工的能动性,导致了精益实施的困难。
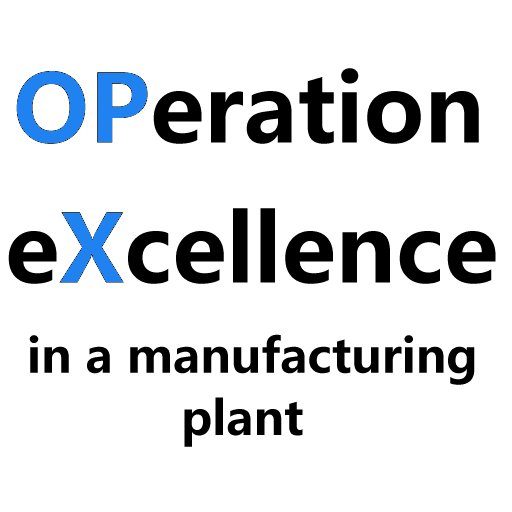
企业存在从顶层战略到日常工作之间的断层。企业负责人可能花了很多精力来规划战略和长远发展目标,但是战略目标没有有效转化为企业年度运营的业绩指标。这样战略目标成了空中楼阁,没有实现的具体路径。同时,断层还体现在战略对年度,季度的工作优先级的错位,可能高层领导希望的是一个方向,但管理人员每天面临的业绩指标又是另外一个方向。加上这些指标又不能合理的分解到各个部门,产线,车间,班组,最终的状况就是战略和日常工作的严重脱节。
企业陷于“唯工具论”,认为精益的工具都是有效万能的,并迷信所谓高端工具的作用,而并没有意识到工具方法和本身业务的结合。典型的现象是企业引入了精益咨询公司,请了很多专家,办了多场精益培训,也培养了自己的黑带和精益大师。可实际企业自身运营的问题,自己员工可能更清楚。问题往往并不是单一复杂问题,一定需要六西格玛专家才能解决。问题往往是一串简单问题的累加,解决这些问题靠的更多是激发实际做这些工作的员工的参与和改进。如果没有这样的渠道和机制,再高级的工具方法也很难落地,发挥效力。
以上是很多企业面临的共同问题和挑战。那么通过了解学习成功实施卓越运营的工厂企业,我们发现有很多可以借鉴参考的经验和最佳实践。这个博客就是希望分享博主30多年的工厂运营经验,希望能对同业者有所帮助。
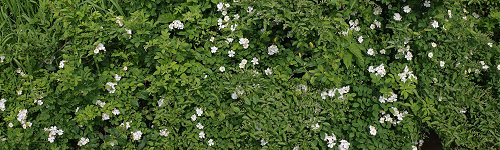